Dieser norddeutsche Fensterhersteller hat in eine neue Oberflächenbeschichtungsanlage für die Fertigung von Holzfenstern und -türen investiert. Nach einem fünfmonatigen Umbau ist jetzt die Inbetriebnahme der ersten Stufe erfolgt.
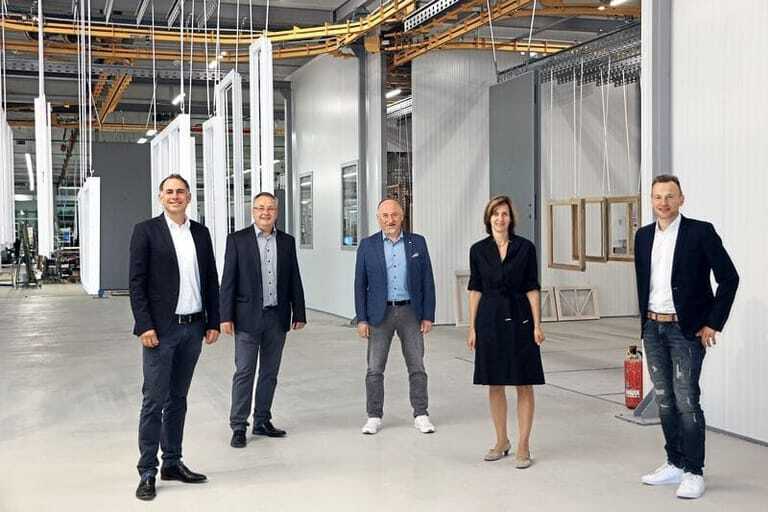
Ein fester Bestandteil der Unternehmensstrategie von Aldra ist die kontinuierliche Weiterentwicklung der Fertigung. Im vergangenen Jahr hat der Hersteller die Entscheidung getroffen, in eine neue Oberflächenbeschichtungsanlage für Holzfenster und -türen zu investieren. „Wir stellen hohe Qualitätsanforderungen an jedes einzelne Bauelement“, erklärt der Geschäftsführer Jan-Peter Albers. Und Holger Asche, Betriebsleiter von Ewitherm in Thedinghausen, ergänzt: „Für die Realisierung unserer Vision fiel die Wahl auf die Firma Range + Heine aus Winnenden und auf den Farblieferanten Remmers.“ Im November 2019 begannen die Umbaumaßnahmen. Neben den Genehmigungsverfahren, die aufgrund baulicher Veränderungen notwendig waren, stellten auch die Corona-Pandemie und der Umbau bei laufendem Betrieb Herausforderungen dar.
Nach nur etwa fünf Monaten Bauzeit konnte jetzt die erste Stufe der Inbetriebnahme erreicht werden. Unterstützt mit moderner Computer- und Robotertechnologie, erstreckt sich die neue Anlage über eine Fläche von 1.600 Quadratmeter. Mit einem Fassungsvermögen der Fördertechnik von maximal 25 Tonnen kann sie bis zu ca. 300 Rahmenteile unterschiedlicher Größen und Formen aufnehmen. Dabei lassen sich Bauelemente von maximal 5.000 mal 3.000 Millimeter in einem Stück beschichten.
In sieben Schritten zum Ergebnis
Die Summe aus sieben Arbeitsschritten garantiert ein langlebiges Ergebnis. Zunächst werden die Elemente für den Imprägnierauftrag durch eine Flutanlage geführt und über die Traverse in eine von zwei Halogentrocknereinheiten gefahren, um die gleichmäßige Trocknung zu ermöglichen. Im nächsten Schritt erfolgt der Auftrag der Grundierung. Hier stehen zwei Flutanlagen bereit – eine zur Grundierung mit Lasurfarben, die sechs Pumpen für einen automatischen Farbwechsel enthält, und eine zur Grundierung deckender Farbtöne. Das System fängt überschüssige Farben auf, die dem Kreislauf wieder zugeführt werden, um den Ressourcenverbrauch zu reduzieren. Damit es zu keiner ungewollten Spannung der Oberflächen kommt, sorgt die Anlage für eine ausreichende Luftfeuchtigkeit.
Im weiteren Schritt erfolgt die erste Lackierung mit einem wasserbasierten Zwischenlack über zwei Roboter im Spritzverfahren. Mit einer 3D-Erkennung ausgestattet, ermitteln sie zunächst die Beschaffenheit, wie z.B. die Profildicke der Elemente, um dann die Farbe gleichmäßig aufzutragen. Nach einer erneuten Trocknung gelangen die Elemente an die Schleifstation. An zwei Arbeitsplätzen erhalten sie einen Zwischenschliff, damit die zweite Finish-Lackierung durch die Roboter optimal ist. Abschließend werden die Elemente in die Entfeuchtungstrocknung mit Umluftfunktion gebracht. Nach der vollständigen Trocknung werden sie mit Beschlägen und Scheiben ausgestattet. Insgesamt fünf Absenkstationen ermöglichen das körpergerechte Arbeiten.
Pflegeleichte Holzqualitäten
Obwohl die finale Abnahme derzeit noch aussteht und sich die Ansteuerung der Leitrechnerfunktion durch die Fensterbausoftware noch in der Umsetzung befindet, überzeugt bereits die hohe Qualität der neuen Oberfläche. „Gemeinsam mit den Partnern Remmers und Range + Heine treten wir dem Vorurteil von pflegeintensiven Holzoberflächen weiter entgegen. Als Beweis dienen unsere hochwertigen Oberflächen der Holz- und Holz/Aluminium-Elemente“, sagt Albers.